Regardless of industry, plastic components must perform safely and reliably. As space and weight limitations continue to encroach upon how these critical goals are met in electrification, OEMs need to find innovative solutions made from equally innovative materials.
What’s changing?
In broadest terms, electrical and electronics devices are seeing significant shifts in:
- Size: The trend toward smaller and more compact devices is challenging designers and manufacturers with how to incorporate advanced technologies into smaller spaces
- Performance: Devices of smaller scale do not equate to less power. Even in larger devices, more power, more features, and greater customer expectations drive performance and component needs
- Space: The combination of size and performance shifts logically impacts the space within which designers, engineers, and manufacturers have to work. As a result, new approaches to component design are emerging that call upon advanced engineering thermoplastics (ETPs) to “create space” through thin-wall constructions that are as safe and reliable as thicker counterparts
Considerations for Thin-Wall Applications
Finding ways to accomplish more in less space is undoubtedly challenging, and further complicated by stringent safety requirements and other specific OEM mandates. Thinner walls are often the key. Finding solutions is possible, but it takes collaboration with skilled materials experts to identify those ETPs that perform at thinner thicknesses.
However, incorporating an ETP that is suitable for constructing thinner walls isn’t a matter of blanket substitution. Take, for example, a common connector. Depending on the device, hundreds — if not thousands — of them could be used in a single application. Injection-molded components with thinner walls may make the fit more comfortable, but it cannot be at the expense of:
- Functionality: In simplest terms, the molded part must function as intended. Features like hinged covers, snap locks, hooks, etc., must consistently deliver to design specifications, without fail
- Safety: The materials selected for molding thin-wall applications must perform to exacting safety standards. Like any other material used, advanced ETPs for thin-wall constructions must have characteristics that ensure flammability rating, electrical insulation, impact strength, heat deflection temperatures, tensile strength, and other key performance requirements are met
Teknor Apex Solutions
Teknor Apex offers custom colorable material solutions used in many electrical and electronics applications to meet requirements concerning:
- UL94 flammability
- High voltage
- Glow wire ignition capability
- Relative thermal index
- Thinner walls in applications such as connectors, sensors, enclosures, and battery packs
Our extensive ETP product portfolio contains versatile Creamid® and Chemlon® polyamides, cross-linkable thermoplastics, and more for applications of varying needs and complexities. Contact us today to learn more and get help meeting your toughest application challenges!
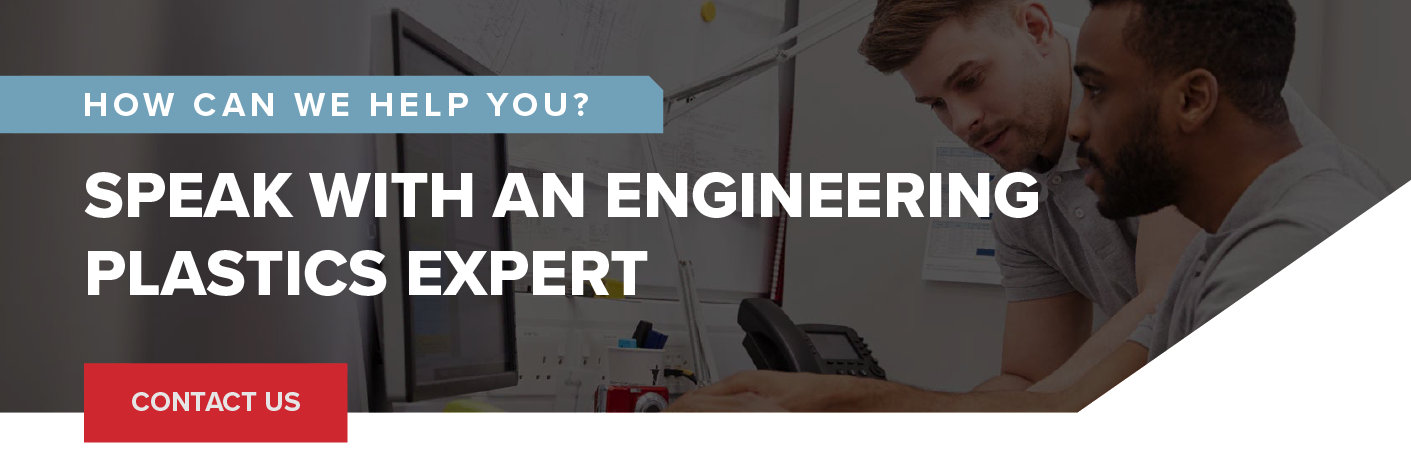